A Tale of Two Projects: Two nearly identical projects with two different delivery methods demonstrate the benefits of using a Collaborative Delivery Method
Our team had the rare opportunity to compare the effects of two different delivery methods on an identical treatment structure. We recently completed renovations at a single plant twice – once using the traditional hard bid method and then several years later using a collaborative progressive design-build method – providing us with valuable insights.
Project #1: Traditional, Design-Bid-Build (Hard Bid) Method
In October 2016, Rogers Water Utilities (RWU) in Rogers, Arkansas, hired Olsson to design a rehabilitation project for their first Bardenpho treatment train. The scope included dewatering and sediment removal of the aeration basin, concrete reinforcement and repair, equipment replacement, electrical work, waterproofing, epoxy coatings, and guardrail and handrail replacement. They procured this project using traditional Design-Bid-Build (Hard Bid) methods and awarded it to the lowest bidder, Crossland Heavy Contractors (CHC), in 2017. The total cost for this project, including engineering fees, was $2.04 Million.
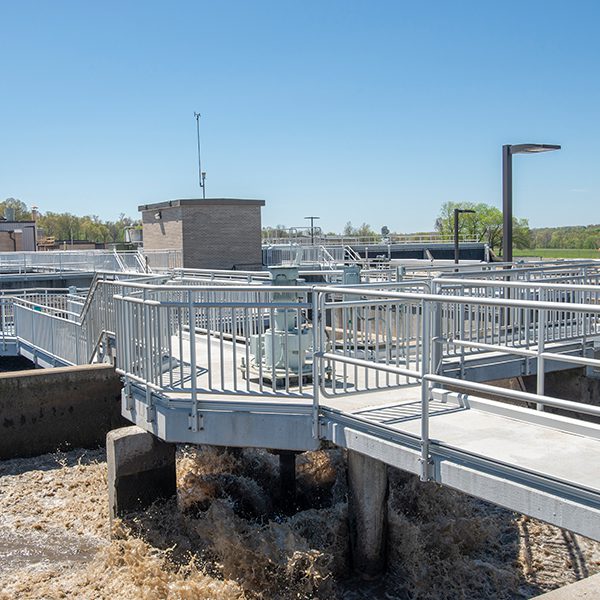
Project 1 Challenge
This project posed a unique challenge due to the uncertainties of what we would find in the aeration basin once construction began. The design team had no way of knowing the necessary repair work that would be needed and did not account for such in the original budget. There were many overruns on the concrete repair due to these unforeseen conditions. The total contract was 660 days.
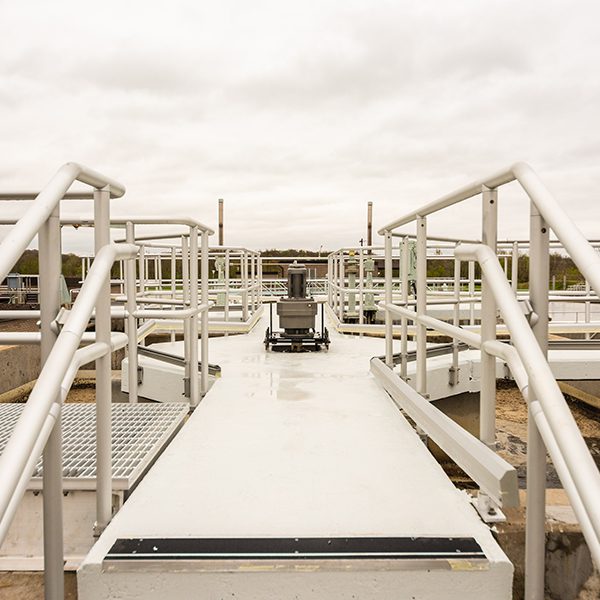
Project #2: Progressive Design-Build
Two years later, the same client was eager to take advantage of Arkansas’s new procurement laws that enabled the use of innovative delivery methods like Design-Build and Construction Management at Risk for public water & sewer projects. This time around, they chose the Progressive Design-Build method.
After a two-step qualifications-based selection process, in January 2020, they selected Crossland Heavy and Olsson as their Progressive Design-Build team.
Same team, same project, different approach with progressive design-build.
Here are our takeaways:
It’s important to note that the scopes of the projects were slightly different. The second progressive design-build project required additional equipment and electrical upgrades for the oxidation ditch aerator and re-air mixer for both treatment trains. The upgrades raised the project cost over the minimum $2M budget required by Arkansas statute to use alternative procurement methods.
See the table below for the two project and delivery method comparisons.
Cost Comparison Highlight | Traditional Design-Bid-Build | Progressive Design-Build |
Concrete Containment Curbs | $23,945.00 | $26,446.00 |
Key Equipment Replacement | $228,053.00 | $221,253.00 |
Concrete Crack Repair | $67.50/LF | $45.00/LF |
Concrete Scour Repair | $44.88/SF | $18/SF |
Structural Concrete Repairs | $114.40/SF | $101.60/SF |
Handrail Replacement | $80.53/LF | $67.40/LF |
Change Orders Processed | 17 | 0 |
Due to significant scope increases, along with the impact of Covid-driven inflation factored in; it’s no surprise that cost went up between the span of the two projects – from $2.04M to $4.64M.
However, one standout benefit of this delivery method was the shortened timeline. Using the Progressive Design-Build method, our team could perform upfront work during preconstruction, cutting down on unforeseen challenges that could potentially stall the schedule.
Project 2 Benefits:
- Utilizing the preconstruction phase allowed us to clean out the basin before the project was designed to ensure any repairs were accounted for and to eliminate overruns of concrete rehabilitation items during construction.
- Early collaboration enables the team to discuss alternative materials and processes, which can result in cost savings, bringing the best value to the overall project.
- Bidding the project at 60% Designed rather than 100% allows for an early GMP (Guaranteed Maximum Price) execution, saving time on the schedule.
- Construction could begin at 90% Designed, giving us the opportunity to procure any long lead time process equipment and begin the structure rehabilitation.
Conclusion: The Construction phase lasted longer on Project 2 due to the increased equipment lead times and covid-delays. However, since construction began during the design phase, the overall timeline was shortened.
Not only does Progressive Design-Build allow for expedited timelines and risk reduction, but it also reduces administrative tasks for the Owner, including the following:
Contract Highlights | Traditional Design-Bid-Build | Progressive Design-Build |
Contracts | 1 for Designer 1 for Contractor | 1 for Design-Builder |
Change Orders | 17 Change Directives | 0 GMP Change Orders |
Contingency | Used for contractor only | The remaining $ is returned to the Owner |
Project 1: Traditional Design-Bid-Build Method (Hard bid)
Through this method, we saved the client almost $30k. Although they had to take on the administrative burden of processing 17 change orders and getting them approved by the council throughout the project duration.
Project 2: Progress Design-Build Method
This open book and transparent process with costs and contingency gave the client peace of mind throughout the project. In the end, there was nearly $200k in contingency remaining which went back into the client’s hands to be used for “wish list items” or miscellaneous improvements that were not in the original scope.
We can work with our clients on which delivery method fits their specific needs best. However, there are major benefits shown to using a collaborative method like Progressive Design-Build, such as:
- Ease of contracting
- Peace of mind through open book cost transparency
- Schedule expediency
- Elimination of change orders
- Collaborative working relationship among all parties
- Transfer of risk from the Owner to the Design-Builder